การตรวจสอบกระบวนการมีความสำคัญต่อความสำเร็จของบริษัทที่ผลิตยา, วัคซีน, ชุดทดสอบและผลิตภัณฑ์ชีวภาพอื่นๆ ทั้งสำหรับคนและสัตว์ ตามแนวทางของ FDA การตรวจสอบกระบวนการคือ “การรวบรวมและประเมินข้อมูลตั้งแต่สถานะการออกแบบกระบวนการจนถึงการผลิตเชิงพาณิชย์ซึ่งสร้างหลักฐานทางวิทยาศาสตร์ว่ากระบวนการสามารถส่งมอบผลิตภัณฑ์ที่มีคุณภาพได้อย่างสม่ำเสมอ”
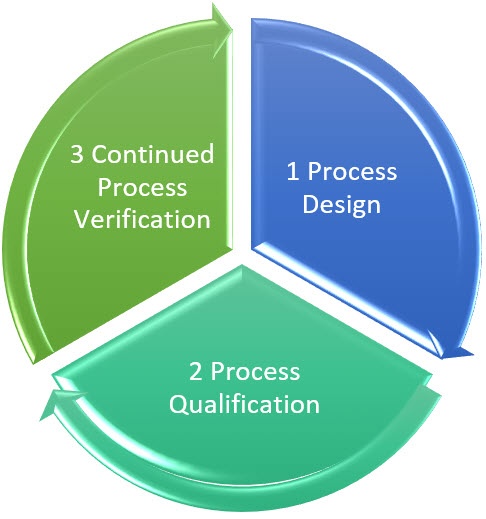
FDA แนะนำสามขั้นตอนสำหรับการตรวจสอบกระบวนการ เรามาสำรวจเป้าหมายของแต่ละขั้นตอนและประเภทกิจกรรม รวมถึงเทคนิคทางสถิติที่มักจะดำเนินการภายใต้กิจกรรม คุณสามารถใช้ซอฟต์แวร์ทางสถิติของ Minitab เพื่อเรียกใช้การวิเคราะห์ใดๆได้ที่นี่ หากคุณยังไม่มี Minitab ทดลองใช้ฟรี 30 วัน
ขั้นตอนที่ 1 การออกแบบกระบวนการ (Process Design)
เป้าหมาย : ออกแบบกระบวนการที่เหมาะสมสำหรับการผลิตเชิงพาณิชย์ตามปกติซึ่งสามารถส่งมอบผลิตภัณฑ์ที่ตรงตามคุณลักษณะด้านคุณภาพได้อย่างสม่ำเสมอ
สิ่งสำคัญที่สุดในขั้นตอนนี้คือการทำความเข้าใจกระบวนการและคุณลักษณะของปัจจัยต่างๆที่มีของกระบวนการในส่วนงานออกแบบ
ตัวอย่าง : การหาพารามิเตอร์ของกระบวนการที่สำคัญในงาน DOE
สมมติว่าเรามีความจำเป็นต้องบ่งชี้ค่าพารามิเตอร์ของกระบวนการผลิตยาเม็ดแบบปลดปล่อยยาทันที (immediate-release tablet) ซึ่งมีพารามิเตอร์ตั้งต้นอยู่ 3 ปัจจัย คือ:
- เปอร์เซ็นต์ฟิลเลอร์ (filler %)
- เปอร์เซ็นต์สลายตัว (disintegrant %)
- ขนาดอนุภาค (particle size)
คุณต้องการหาค่าการตั้งค่า(setting) ของทั้ง 3 ปัจจัยนี้ว่าควรมีค่าเท่าไหร่เพื่อทำให้เปอร์เซ็นต์การละลายที่ 30 นาทีมีค่ามากที่สุด การออกแบบการทดลอง (DOE) ซึ่งจะให้ได้แผนการเก็บข้อมูลที่มีประสิทธิภาพ ปรับเปลี่ยนค่าพารามิเตอร์ตั้งต้นที่เหมาะสมเพื่อให้สัมพันธ์กับค่าผลลัพธ์ที่ต้องการศึกษา เมื่อทำการเก็บข้อมูลและทำการวิเคราะห์เพื่อหาพารามิเตอร์ตั้งต้นที่สำคัญแล้ว ยังมีการใช้ DOE เพื่อหาการตั้งค่าที่เหมาะสมที่สุดได้ด้วย (หากต้องการเรียนรู้เพิ่มเติมเกี่ยวกับ DOE ลองอ่าน 8 Expert Tips for Excellent Designed Experiments)
การทำการทดลอง (Running the Experiment): ขั้นตอนแรกของการทำ DOE คือการกำหนดปัจจัยตั้งต้นและช่วงของค่าพารามิเตอร์ที่ต้องการศึกษา ขั้นตอนต่อไปคือสร้างออกแบบการทดลองเพื่อจะนำไปเก็บข้อมูลตามแผน
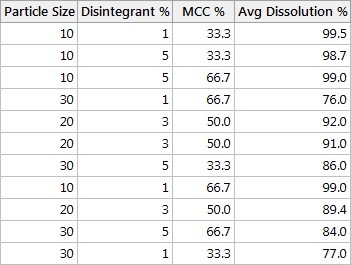
จากผลการออกแบบตามที่แสดงด้านล่างนี้ เราใช้ค่า:
- ขนาดอนุภาค (particle size) = 10
- เปอร์เซ็นต์สลายตัว (disintegrant %) = 1%
- MCC = 33.3%
จากนั้นเราจะบันทึกค่า เปอร์เซ็นต์การละลาย (dissolution%) เฉลี่ยโดยแต่ละแบชใช้ยาทั้งหมด 6 เม็ด

การวิเคราะห์ข้อมูล (Analyzing the Data ): ใช้คำสั่งวิเคราะห์ DOE และค่า p-value ตอนนี้เราพร้อมแล้วที่จะบ่งชี้ว่าปัจจัยตั้งต้นใดสำคัญ จากกราฟ แท่งกราฟที่เกินเส้นนัยสำคัญ(เส้นสีแดง)บนกราฟ Pareto Chart คือ
particle size, disintegrant% รวมทั้งอิทธิพลร่วม(interaction) ของ 2 ปัจจัยนี้ด้วย ส่วน MCC%(Filler%) ไม่มีนัยสำคัญ
การหาจุดที่ทำให้เกิดคุณภาพที่เหมาะสม (Optimizing Product Quality) : ตอนนี้เราได้ระบุปัจจัยตั้งต้นสำคัญ แสดงว่าเราพร้อมที่จะทำการหาค่าการตั้งค่าที่เหมาะสมของปัจจัยตั้งต้นนั้นๆได้แล้ว จาก Contour plot เราสามารถกำหนดจุดที่เหมาะสมของค่า particle size และ disintegrant% เพื่อทำให้ได้ค่า %dissolution มีค่า 80% หรือมากกว่า
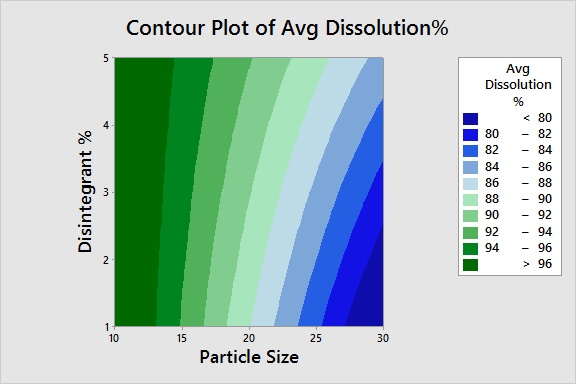
ขั้นตอนที่ 2 การตรวจรับรองกระบวนการ (Stage 2: Process Qualification)
เป้าหมาย : ประเมินการออกแบบกระบวนการเพื่อตรวจสอบว่าสามารถผลิตเชิงพาณิชย์ซ้ำได้หรือไม่ การผ่านขั้นตอนที่ 2 เป็นสิ่งที่จำเป็นก่อนการผลิตในเชิงพาณิชย์
ตัวอย่าง 1 : ประเมินเกณฑ์การยอมรับด้วยการวิเคราะห์ความสามารถ
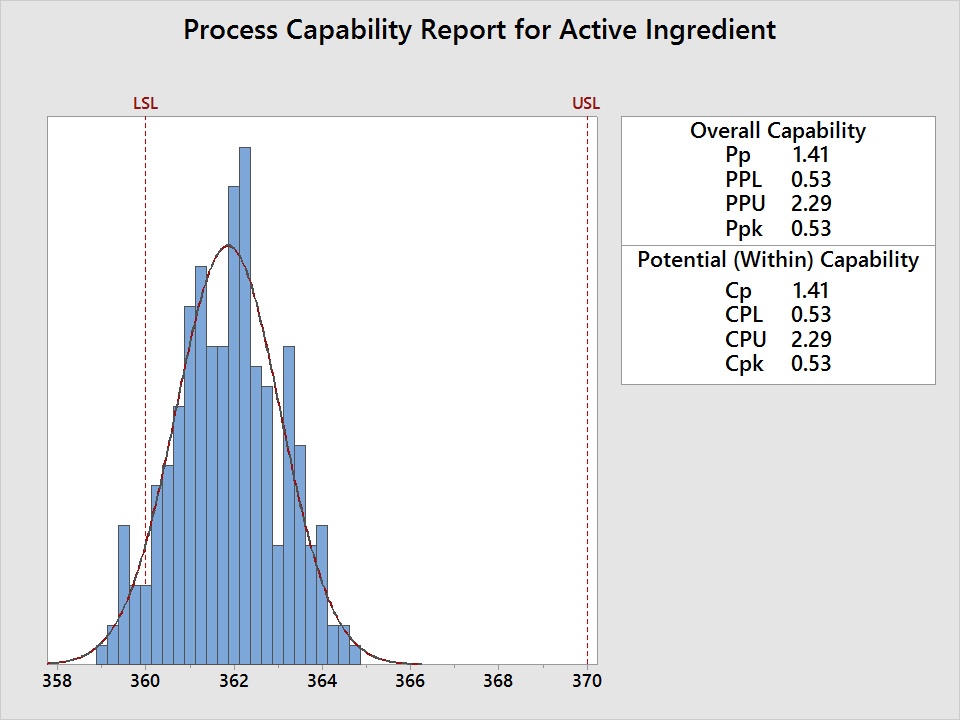
สมมติว่าตัวยาที่ออกฤทธิ์ในยาคลายเครียด (tranquilizer) ต้องมีปริมาณอยู่ระหว่าง 360 ถึง 370 mg/mL และคุณต้องการประเมินระดับคุณภาพด้วยการกำหนดเกณฑ์ไว้ว่าค่า Cpk ควรได้อย่างน้อยเท่ากับ 1.33 ในการประเมินประสิทธิภาพของกระบวนการด้วยการดูค่าวัดเทียบกับข้อกำหนดเฉพาะ ซึ่งในการวิเคราะห์ความสามารถจะใช้โปรแกรม Minitab ทำการสุ่มเลือกยาจำนวน 50 แบตช์ และในแต่ละแบตช์เลือกสิ่งตัวอย่างจำนวน 5 ตัวอย่าง จากนั้นทำการวัดตัวยาที่ออกฤทธิ์ในสิ่งตัวอย่าง ทำการวิเคราะห์ข้อมูลโดยเทียบเคียงว่ามีค่าระหว่าง 360 ถึง 370 mg/mL
ผลการวิเคราะห์ความสามารถของกระบวนการพบค่า Cpk เท่ากับ 0.53 ซึ่งไม่ผ่านเกณฑ์การยอมรับ 1.33 ปริมาณตัวยาที่ออกฤทธิ์ในการคลายเครียดไม่ผ่านตามเกณฑ์ แล้วเราจะทำการปรับปรุงได้อย่างไร
ค่า Cp ที่ได้คือ 1.41 และจากกราฟจะเห็นได้ว่าความผันแปรนั้นอยู่ในเกณฑ์ที่ยอมรับได้เพราะอยู่ในช่วงของข้อกำหนดเฉพาะ ส่วนค่าเฉลี่ยของกระบวนการควรต้องปรับให้มีค่ามากขึ้นเพื่อทำให้ได้ค่า Cpk เป็นไปตามเกณฑ์
ตัวอย่าง 2 : การวิเคราะห์ความผันแปรที่เกิดขึ้นระหว่างแบตช์ด้วย Boxplot
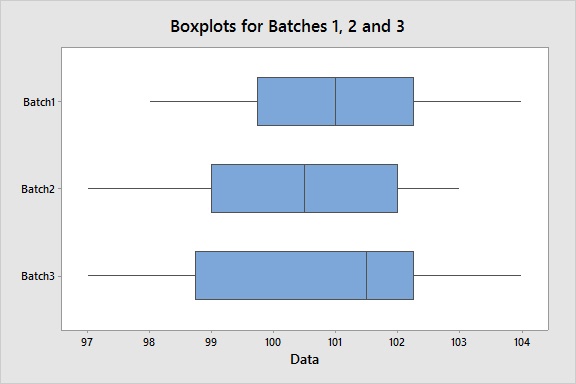
สมมติว่าเราต้องการประเมินความสม่ำเสมอซึ่งเป็นคุณสมบัติเชิงคุณภาพที่สำคัญ ด้วยการเลือกมา 3 แบตช์จาก 10 แหล่ง เพื่อทำการตรวจสอบความผันแปรภายในแบตช์เดียวกัน และความผันแปรที่แบตช์ต่างกัน โดยเราจะใช้ boxplots เพื่อดูความผันแปรในแต่ละแบตช์ ซึ่งสามารถช่วยเราให้เห็นภาพได้ชัดเจนขึ้นในการประเมินความผันแปรทั้งภายในแบตช์เดียวกันและระหว่างแบตช์ รวมทั้งยังเห็นด้วยว่ามี outlier เกิดขึ้นหรือไม่ โดย Minitab จะแสดง outlier ด้วยการกำกับสัญลักษณ์ (*) ไว้ในแผนภาพ
แม้ว่า boxplot จะเป็นเครื่องมือที่มีประโยชน์ในการประเมินด้วยสายตา แต่เรายังสามารถประเมินทางสถิติได้ว่าความแตกต่างระหว่างแบตช์แตกต่างอย่างมีนัยสำคัญหรือไม่โดยใช้การทดสอบความแปรปรวน การทดสอบแสดงค่า p-value ที่มากกว่าระดับนัยสำคัญ 0.05 (หรือระดับนัยสำคัญที่คุณต้องการ) ซึ่งสนับสนุนข้อสรุปว่ามีความเสถียรระหว่างแบตช์
ตัวอย่าง 3: การประยุกต์ใช้ช่วงค่าเผื่อ
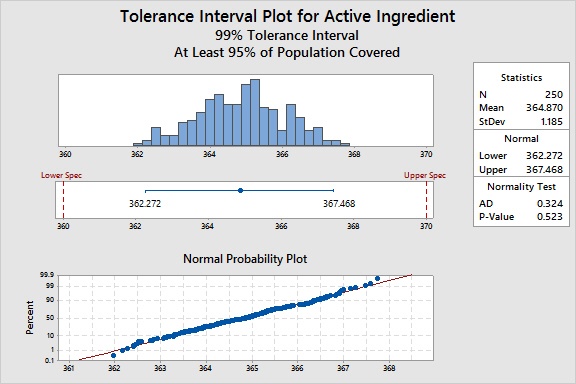
เครื่องมือที่มีประโยชน์อีกอย่างสำหรับขั้นตอนการตรวจรับรองกระบวนการคือช่วงค่าเผื่อ เครื่องมือนี้ประยุกต์ใช้ได้หลากหลาย ตัวอย่างเช่นสามารถใช้ช่วงค่าเผื่อเพื่อเปรียบเทียบกระบวนการของคุณกับข้อกำหนด, รายละเอียดผลลัพธ์ของกระบวนการหรือสร้างเกณฑ์การยอมรับ
สำหรับคุณลักษณะเฉพาะของผลิตภัณฑ์ช่วงค่าเผื่อจะให้ช่วงของค่าที่น่าจะครอบคลุมสัดส่วนที่ระบุของประชากร (เช่น 95%) สำหรับระดับความเชื่อมั่นที่ระบุ (เช่น 99%)
ตัวอย่างเช่นสมมติว่าเราต้องการทราบว่าค่าของสารออกฤทธิ์ในกระบวนการผลิตเปรียบเทียบกับข้อกำหนด คือ 360 ถึง 370 mg/mL เป็นอย่างไร
จากชุดข้อมูลดังกล่าว ผลการวิเคราะห์จาก Minitab เราพบว่าที่ความเชื่อมั่น 99% ใน 95% ของปริมาณตัวยามีค่าระหว่าง 362.272 ถึง 367.468 mg/mL จากขอบเขตของค่าที่ได้บ่งชี้ว่ากระบวนการนี้จะสามารถทำได้ตามข้อกำหนด (360 ถึง 370) เราจึงสรุปว่า ด้วยความเชื่อมั่นระดับสูงกระบวนการมีความผันแปรน้อยกว่าค่าที่อนุโลมไว้ในข้อกำหนดหรือบางครั้งเราต้องประเมินความสม่ำเสมอของตัวยา (content uniformity) โดยใช้ความเชื่อมั่น 99% ที่ครอบคลุม 99% ของทั้งหมด เราใช้ยา 30 เม็ดจากนั้นทำการหาช่วงค่าเผื่อ ซึ่งพบว่าด้วยความเชื่อมั่น 99% มียา 99% จากที่ทำการทดสอบมีความความสม่ำเสมอของตัวยาในช่วงที่กำหนด โดยการวิเคราะห์ด้วย Minitab
ขั้นตอนที่ 3: การยืนยันความถูกต้องกระบวนการผลิตอย่างต่อเนื่อง
เป้าหมาย: ให้การประกันอย่างต่อเนื่องว่ากระบวนการยังคงอยู่ในสถานะของการควบคุม – สถานะที่ผ่านการตรวจสอบ – ระหว่างการผลิตเชิงพาณิชย์
ตัวอย่าง: การเฝ้าระวังกระบวนการผลิตด้วยแผนภูมิควบคุม
สมมติว่าคุณได้รับมอบหมายให้เฝ้าดูกระบวนการผลิตเม็ดยาที่ใช้กิน (oral tablet) ซึ่งคุณจะต้องแสดงให้เห็นว่าความแข็งของเม็ดยานั้นจะคงที่ได้ตลอด และตรวจจับความผันแปรของกระบวนการผลิตถ้าเกิดมีการเปลี่ยนแปลงขึ้นจะต้องมีการดำเนินการบางอย่าง
รวมทั้งยังต้องทำให้มั่นใจได้ว่าการผลิตนั้นพนักงานไม่ได้ปฏิบัติการมากจนเกินพอดีต่อความผิดปกติเล็กๆน้อยๆ ซึ่งเกิดขึ้นเป็นปกติ เพราะการทำเช่นนั้นอาจทำให้ความผันแปรเพิ่มขึ้นได้
คุณทำการเลือกยาตัวอย่างมาจำนวน 5 เม็ดภายในการผลิตทุกๆหนึ่งชั่วโมง ทำการวัดค่าความแข็งของเม็ดยา จากนั้นใช้โปรแกรม Minitab สร้างแผนภูมิ Xbar-R
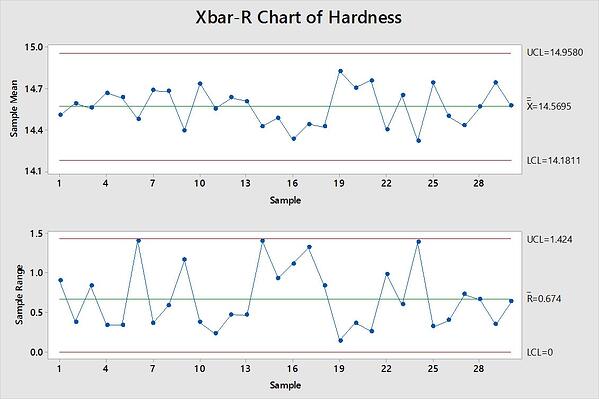
จากแผนภูมิ Xbar-R ไม่พบว่ามีจุดแดงใดใดที่บ่งชี้ความผิดปกติ หมายความว่ากระบวนการผลิตอยู่ภายใต้สภาวะการควบคุม (in control) ซึ่งทำให้สรุปได้ว่าคุณสามารถรักษาให้กระบวนการผลิตอยู่ในสภาวะเดียวกับตอนที่ได้รับการตรวจสอบความถูกต้อง และไม่มีการเปลี่ยนแปลงใดใดของค่าเฉลี่ยกระบวนการ (ดูได้จากแผนภูมิ Xbar ที่แสดงไว้ด้านบน) หรือ ความผันแปรเองก็ไม่มีการเปลี่ยนแปลงเช่นกัน (ดูได้จากแผนภูมิ R)
ถ้าในแผนภูมิควบคุมแสดงให้เห็นว่ามีสภาวะไม่อยู่ภายใต้การควบคุม (out-of-control state) –กระบวนการมีความผันแปรจากแหล่งที่ไม่ได้รับการควบคุม- เราจะต้องดำเนินการหาสาเหตุที่เกิดความผันแปรนั้น อาจจะมีการเปลี่ยนแปลงคุณสมบัติของวัตถุดิบ มีการบำรุงรักษาเครื่องมือหรือปรับเทียบเครื่องมือหรือไม่ หรือ แหล่งความผันแปรอื่นที่ส่งผลต่อค่าเฉลี่ยทำให้มีค่าเปลี่ยนไป
สรุป
การเฝ้าระวังกระบวนการด้วยตรวจจับความผันแปรของกระบวนการ สามารถใช้แผนภูมิควบคุมได้เป็นอย่างดี แต่ยังมีเครื่องมือทางสถิติอย่างอื่นๆที่นำมาใช้ในการออกแบบกระบวนการและการตรวจรับรองกระบวนการ เทคนิควิธีทางสถิติที่ช่วยสนับสนุนการทำงานในงานตรวจสอบความถูกต้องของกระบวนการ ตัวอย่างเช่น การชักสิ่งตัวอย่างเพื่อการยอมรับ (acceptance sampling) เพื่อช่วยในการคำนวณหาจำนวนสิ่งตัวอย่างที่ต้องสุ่มเพื่อตรวจสอบและตัดสินใจว่าจะปฏิเสธหรือยอมรับลอต เป็นต้น
บทความต้นฉบับ : Process Validation Tools For Clinical Approval: An Example For Passing the 3 FDA Stage Goals
ต้นฉบับนำมาจาก Minitab blog, แปลและเรียบเรียงโดยชลทิชา จำรัสพร
บริหารจัดการ SCM Blog โดยชลทิชา จำรัสพร บริษัท โซลูชั่น เซ็นเตอร์ จํากัด ตัวแทน Minitab ในประเทศไทย

เพิ่มเติมเกี่ยวกับบริษัท Minitab
Minitab ช่วยให้บริษัทและองค์กรต่างๆ สามารถมองเห็นแนวโน้มของข้อมูล, แก้ปัญหาและค้นพบประเด็นสำคัญจากข้อมูลเชิงลึก โดยนำเสนอชุดโซลูชั่นที่ครอบคลุมทุกด้านและดีที่สุดสำหรับซอฟต์แวร์ในระดับเดียวกัน ที่ใช้สำหรับการวิเคราะห์ข้อมูลและการปรับปรุงกระบวนการ
ด้วยวิธีการที่เป็นเอกลักษณ์ และการนำเสนอซอฟต์แวร์และบริการแบบองค์รวม Minitab ช่วยให้องค์กรเข้าถึงกระบวนการตัดสินใจในส่วนที่ช่วยผลักดันให้เกิดความเป็นเลิศทางธุรกิจได้ดีขึ้น ความง่ายในการใช้งานที่โดดเด่นกว่าใครมีส่วนช่วยให้ Minitab สามารถทำให้การเข้าถึงข้อมูลเชิงลึกเป็นเรื่องที่ง่าย ทีมงานของ Minitab ซึ่งประกอบด้วยผู้เชี่ยวชาญทางด้านการวิเคราะห์ข้อมูลที่ได้ผ่านการอบรมมาเป็นอย่างเข้มงวด จะช่วยให้ผู้ใช้งานมั่นใจว่าจะได้รับประโยชน์สูงสุดจากการใช้งานวิเคราะห์ข้อมูลและพร้อมที่จะให้คำปรึกษาตลอดเวลาที่ใช้งานเพื่อนำไปสู่การตัดสินใจที่ดีขึ้น รวดเร็ว และแม่นยำ
เป็นเวลากว่า 50 ปีที่ Minitab ได้ช่วยองค์การต่าง ๆ เพิ่มรายได้ ควบคุมและลดต้นทุน เพิ่มคุณภาพ เสริมสร้างความพึงพอใจของลูกค้า และเพิ่มประสิทธิภาพ ธุรกิจและองค์นับหมื่นทั่วโลกใช้ Minitab Statistical Software®, Companion by Minitab®, Minitab Workspace®, Salford Predictive Modeler® and Quality Trainer® เป็นเครื่องมือช่วยในการค้นพบและปรับปรุงความบกพร่องในกระบวนการ